The Effects of Vibrotactile Feedback on Task Performance in a 3D-printed Myoelectric Prosthetic Arm
(1) The Westminster School, Atlanta, Georgia
https://doi.org/10.59720/19-052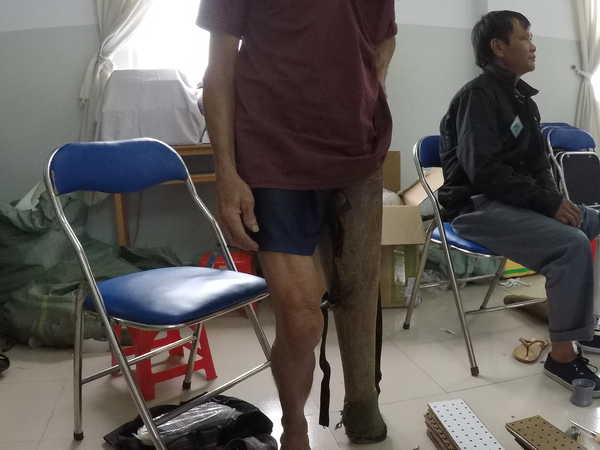
The lack of tactile feedback in today’s hand prosthetics complicates the user experience by forcing a user to visually confirm that the prosthetic is grasping an object. This study strives to remedy both the financial and mechanical deficiencies in current prosthetics through building a simple, noninvasive, vibratory sensory feedback system into an inexpensive constructed 3D-printed prosthetic arm. This 3D-printed prosthetic arm was designed in SolidWorks and printed to the specifications of a participant with a left forearm amputation. The myoelectrical components include a muscle sensor that sends electrical signals to an Arduino microcontroller, which translates the data into code orders to trigger a servo motor to open or close the hand. Vibrotactile feedback was implemented by using a touch sensor on the tip of the index finger of the prosthetic that activates a vibrating motor attached to the residual arm. To test the efficacy of the sensory feedback, the participant was asked to perform a series of tasks both with and without the vibrotactile feedback, both blindfolded and non-blindfolded. The presence of vibrotactile feedback was essential for completing blindfolded tasks, but it did not assist in improving non-blindfolded task performance. The total cost of materials to build this prosthetic arm was $158.46. This study supports the hypothesis that the simple sensory vibrotactile feedback system in the design of this 3D-printed myoelectric prosthetic arm has the potential to enhance sensory feedback performance of amputees by decreasing visual dependency, at a fraction of the cost of a custom-designed myoelectric prosthetic.
This article has been tagged with: